SURFACE FINISHING
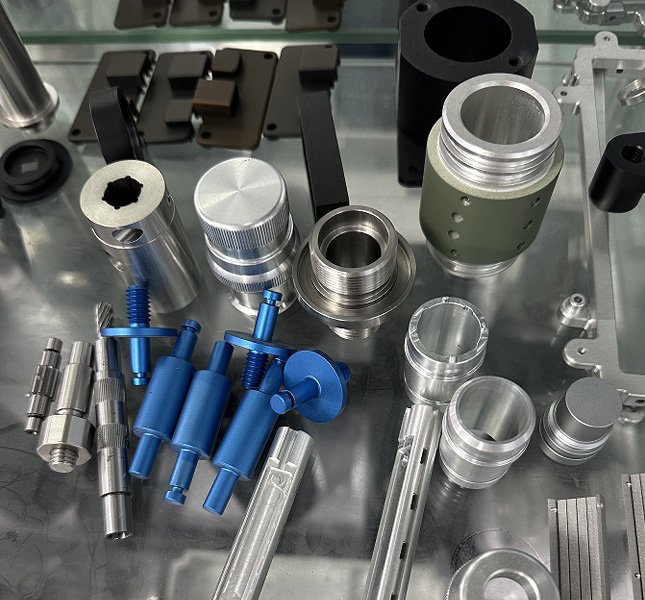
Premium Surface Finishing Service
* Material type (aluminum, steel, brass, etc.)
* Intended use (outdoor, medical, decorative, etc.)
* Desired appearance and feel Required durability or conductivity
Best You Need, Best We Provide!
Different Surface Finishing for Various Metal Surfaces
The standard finish of a part refers to its initial surface appearance right after manufacturing—whether it’s been ejected, machined, printed, or cast. At this stage, the part typically shows visible tooling marks, and may retain traces of resin, powder, or other materials depending on the production process used.
CNC Machined Parts
CNC machined parts often undergo surface treatments to boost corrosion resistance, increase durability, and enhance visual appeal. Processes such as anodizing, plating, and powder coating help shield components from environmental wear, minimize friction, and extend service life. They are essential to ensure consistent performance of precision parts in high-demand sectors like aerospace and automotive.
Rapid Tooling Parts
Surface treatments play a crucial role in rapid tooling by enhancing durability and minimizing wear during high-speed production. Coatings such as nitriding or chrome plating reduce friction, improve mold release, and increase surface hardness. These enhancements help ensure consistent part quality, extend tool lifespan, and maintain accuracy in prototyping and short-run manufacturing.
3D-Printed Parts
3D-printed parts typically have rough surfaces that require post-processing methods such as sanding, coating, or chemical smoothing to enhance both appearance and strength. These surface treatments improve resistance to moisture, UV exposure, and chemicals. As a result, the parts meet both functional and aesthetic standards required in applications like medical devices and consumer products.
Die-Casted Parts
Die-cast parts require surface treatments to protect against corrosion, boost durability, and enhance their appearance. Techniques such as electroplating and powder coating apply protective coatings, increase surface hardness, and create smooth finishes. These treatments are vital for high-volume components in industries like automotive and electronics, where both performance and aesthetics are crucial.
Sheet Metal Fabrications
Surface treatments are essential for sheet metal fabrications to prevent rust, promote better paint adhesion, and increase durability. Methods such as galvanizing, powder coating, and anodizing form protective barriers against environmental damage, ensuring long-lasting performance in applications like construction and HVAC systems, while delivering a polished and attractive appearance.
Extruded Parts
Extruded components, commonly crafted from aluminum or plastics, benefit from surface treatments such as anodizing or powder coating to enhance corrosion resistance and surface hardness. These processes also improve their visual appeal and wear resistance, making them ideal for applications in architecture, automotive, and industrial sectors where both durability and finish are essential.
From Design To Prototyping To Production
The look and quality of a part are just as crucial as its function and performance. At FUTURE PRECISION, our surface finishing services guarantee that every component—whether metal, composite, or plastic—meets the highest standards of both appearance and functionality.
* ISO 9001:2015 Certified Quality Management System;
* Precision CMM Quality Inspections;
* Comprehensive One-Stop Service.
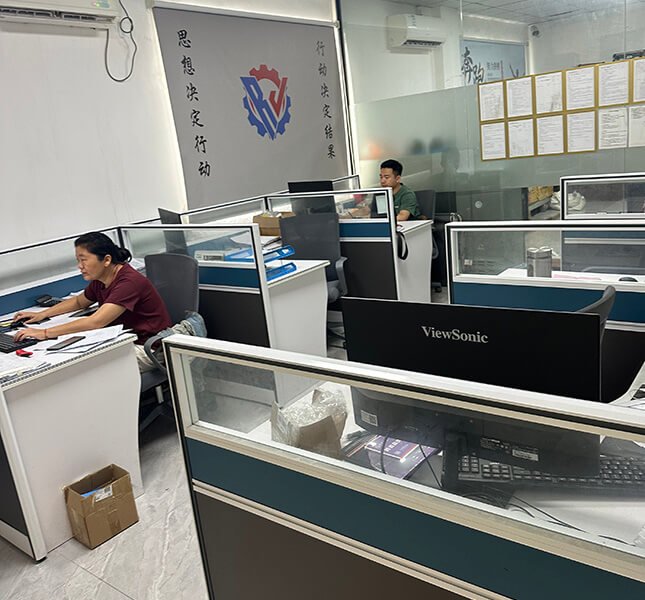
Tailor Your Surface Finishing Solution
Bespoke Surface Finishing Solutions
Rapid Prototyping
We provide top-quality rapid prototyping services in China, offering competitive pricing on surface finishes and expedited delivery. Utilizing the latest rapid prototyping technologies, we collaborate closely with you to refine and validate your product’s surface treatments, perform functional testing, and complete engineering verification to meet your design requirements.
Rapid Manufacturing
FUTURE PRECISION is your trusted partner for surface finishing manufacturing in China. We provide a comprehensive range of services, from efficient rapid prototyping to full-scale production of surface-finished parts. With extensive machining expertise and strong resource integration capabilities, our company is equipped to handle projects of any scale, ensuring your parts achieve the highest quality standards.
Custom CNC Machining
We offer comprehensive rapid surface finishing solutions along with affordable custom surface treatment and machining services. Whether you require production-grade materials, intricate geometries, tight tolerances, or fine details, partnering with KeSu surface finishing factory ensures you receive parts that meet your exact specifications throughout the design, prototyping, and manufacturing stages.
OUR HAPPY CUSTOMERS
We’ve Helped Thousands of Customers Achieve Success.
Selecting the Right Prototype Manufacturer. Enjoy personalized one-on-one support from our expert technical team, with fast responses within hours. We offer the most competitive prices in the market—up to 30% lower than those in Europe and the Americas.
Surface Finish Categories
Surface Treating | Details |
---|---|
Polishing | Materials: Aluminum, Stainless Steel, Brass; Surface Roughness: Ra 0.8μm – 32μm |
Grinding | Applicable to Aluminium, Stainless Steel, Brass. Achieves a surface roughness of Ra0.63-0.01μm. |
Brushing | Applicable to Aluminium, Stainless Steel, Brass. Achieves a surface roughness of Ra1.2μm-Ra47μm. |
Sandblasting | Applicable to Aluminium, Steel, Stainless Steel, Brass, Bronze, Copper, Titanium, Magnesium, ABS, HDPE, Nylon, PC, POM, PMMA, PTFE. Matte finish, thickness 1-100μm, roughness Ra10μm-60μm. |
Painting | Applicable to Aluminium, Steel, Stainless Steel, ABS. Available in Black or any RAL code/Pantone number. Thickness 10-100μm. |
Powder Painting | Applicable to Aluminium, Steel, Stainless Steel, ABS. Available in Black or any RAL code/Pantone number. Thickness 50-150μm. |
Anodizing | Applicable to Aluminium. Available in black, clear, or any RAL code/Pantone number. Thickness 4-8μm (clear), 8-12μm (color). |
Hard Anodized | Applicable to Aluminium. Available in Black, Clear. Thickness 25-50μm. |
Passivation | Applicable to Steel, Stainless Steel, Brass. Thickness 1-10μm. |
Zinc Plating | Applicable to Steel, Stainless Steel, Brass, Bronze. Available in Clear, Black, Colourful. |
Nickle Plating | Applicable to Aluminium, Steel, Stainless Steel, Brass, Bronze, Copper. Clear finish, thickness 6-100μm. |
Chrome Plating | Applicable to Aluminium, Steel, Stainless Steel, Brass, Bronze, Copper. Available in Clear, Black. Thickness 1-3μm (Cosmetic), 50-100μm (Hard). |
Blacken/Black Oxide | Applicable to Steel, Stainless Steel. Black finish, thickness 0-30μm. |
Black & Zinc | Applicable to Steel, Stainless Steel, Brass, Bronze. Black finish. |
Teflon Coating | Applicable to Aluminium, Steel, Stainless Steel. Black finish. |
Titanium Coating | Applicable to Stainless Steel. Available in Gold, White, Bronze, Silver, Black, Blue, Rose, Purple. Thickness 0.1μm-5μm. |
DLC Coating | Applicable to Steel. Black finish, thickness 1-4μm. |
Laser Marking | Applicable to Aluminium, Steel, Stainless Steel, Brass, Bronze, Copper, Titanium, Magnesium, ABS, HDPE, Nylon, PC, POM, PMMA, PTFE. Available in Black, White, Grey, and other colors. |
Silk Screen | Applicable to Aluminium, Steel, Stainless Steel, Brass, Bronze, Copper, Titanium, Magnesium, ABS, HDPE, Nylon, PC, POM, PMMA, PTFE. Available in Black or any RAL code/Pantone number. |
Transfer Printing | Applicable to Stainless Steel, Metal with Coating, ABS, PE, PP. Available in any RAL code/Pantone number. |
Micro Arc Oxidation | Applicable to Aluminium, Magnesium, Titanium. Available in Black, Grey. |
Surface Treatment FAQs
What is Surface Finishing?
Surface finishing refers to the process of modifying a material’s surface to improve its appearance, enhance durability, increase corrosion resistance, or achieve other functional benefits. Common techniques include polishing, plating, anodizing, and various coating methods.
What are the Most Common Surface Finishing Techniques?
Popular methods include electroplating, powder coating, anodizing, polishing, sandblasting, and painting. The right technique depends on the material and the intended performance or aesthetic requirements.
Why is Surface Finishing Important?
Surface finishing enhances the visual appeal of a part, protects it from corrosion and wear, improves properties like electrical conductivity and friction resistance, and ultimately extends the component’s lifespan.
Which Materials can be Surface Finished?
A wide range of materials can undergo surface finishing, including metals (such as steel, aluminum, and copper), plastics, wood, and ceramics. The specific method chosen depends on the material’s characteristics.
How do I Select the Right Surface Finishing Method?
Key factors include the base material, the operating environment (e.g., indoor or outdoor use), aesthetic goals, required durability, and budget. Consulting with a surface finishing expert can help ensure the best results.
Is Surface Finishing Environmentally Friendly?
While some methods, like electroplating, involve chemicals that must be handled responsibly, many modern techniques—such as water-based coatings and eco-friendly finishes—are designed to minimize environmental impact.
How Long does Surface Finishing Take?
Lead time varies by process, part size, and complexity. Basic finishes like polishing can be completed in a few hours, whereas more involved methods like electroplating or powder coating may take several days.
Can Surface Finishes be Repaired?
In many cases, yes. Finishes such as coatings or polished surfaces can often be reapplied or restored. However, repair options depend on the type of damage and the original finishing process.
Request a Quote to Launch Your Surface Finishing Project
From prototyping to full-scale production, our comprehensive surface finishing services deliver exceptional quality, fast turnaround times, and competitive pricing.