RAPID TOOLING
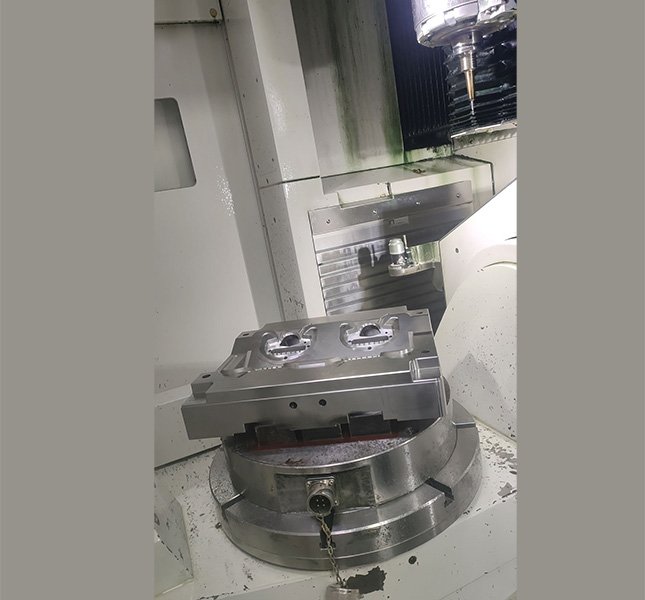
Rapid Tooling Service
Rapid Tooling is a manufacturing process that quickly creates molds, dies, or tools used in production, often using additive manufacturing (3D printing) or other fast prototyping methods. In essence, rapid tooling helps companies bring products to market faster by speeding up the tool-making phase.
Best You Need, Best We Provide!
What We Good At Rapid Tooling Processes
To deliver rapid results, certain limitations apply to the types of tools and parts that can be produced using this method. These constraints don’t compromise the quality of the tool; instead, they streamline the development process to minimize production lead times and reduce costs.
Enhanced Simplicity
Rapid tooling involves two-piece molds, typically with no more than two cavities per mold. These molds do not include additional sliders or hand-loaded inserts, making them ideal for simpler geometries. As a result, complex gate/runner systems or advanced cooling channels are not required, allowing for straightforward ejector pin strategies and faster production.
Surface Treatment
Rapid tools generally feature as-machined surfaces with minimal polishing or bead blasting. We offer surface finishes for molded parts based on the Plastics Industry Association’s standard classification system, ensuring consistent quality and appearance.
Quick Feedback
Upload your 2D drawings or 3D models, and receive detailed quote feedback within 24 hours. Our experienced engineers will review your design to eliminate miscommunication, consult with you as needed, and provide a cost-effective solution tailored to your project.
Premium Quality
Our commitment to quality is reflected in every stage of production—from material selection and rapid tooling to surface finishing and CMM inspection. With a rigorous, detail-oriented approach, we ensure consistent quality from prototype to final production. Each part is carefully inspected before delivery—no shortcuts, no compromises.
Rapid Delivery
By combining skilled rapid tooling techniques with an experienced quoting team, we streamline production for quicker turnaround. Orders are prioritized based on complexity and urgency, ensuring your project is delivered on time.
Fast Support
From quotation to final delivery, every customer is supported by a dedicated technical contact. We provide quick, clear responses to your questions and keep you updated at every step—ensuring peace of mind and satisfaction with the final product.
Why Choose Us as Your Rapid Tooling Partner?
FUTURE PRECISION’s rapid tooling services are tailored to meet the needs of clients worldwide. Our rapid tooling solutions offer low costs and quick turnaround times, allowing you to identify and resolve design issues early—before mass production begins. This enables your engineering and R&D teams to visually inspect prototypes, make necessary adjustments to drawings, and ultimately enhance the durability of your production tooling. Our Advantages:
* Consistent standard tolerances;
* Competitive pricing suitable for every project;
* State-of-the-art industry-leading equipment
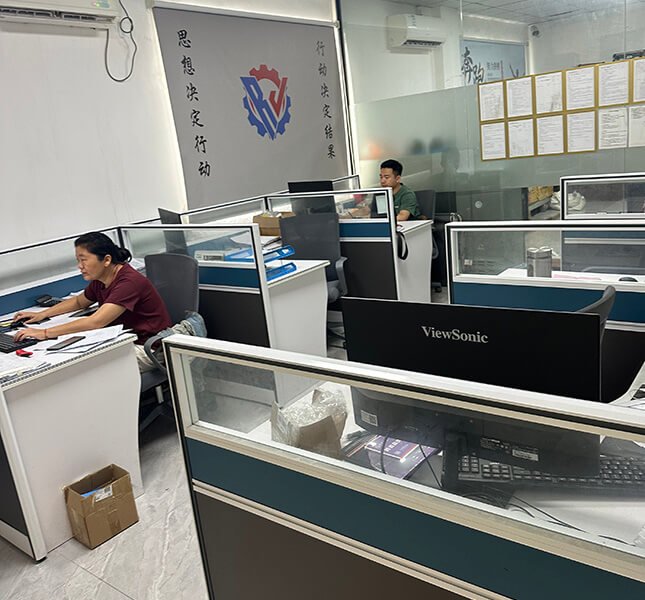
Customize Your Rapid Tooling Service Solution
Premium Rapid Tooling Services
CNC Machining
We provide precise CNC machined parts to bring your designs or concepts to life, with quantities ranging from 1 to 500+ pieces. Our comprehensive CNC services include milling, turning, wire cutting, laser cutting, EDM, laser engraving, and more—ensuring accuracy and fast turnaround.
Vacuum Casting
Vacuum casting uses a master prototype to create a silicone mold, into which material is poured to produce parts. This method offers quick turnaround and cost-effective production for quantities from 1 to 100+ pieces, ideal for converting your design concepts into functional parts.
3D Printing
As the fastest and most affordable rapid tooling method, we offer six different 3D printing technologies to suit various needs—from low-cost, ultra-fast prototypes to high-quality parts designed for functional testing.
Making our customers happy is what drives us.
We’ve helped thousands of clients succeed.
Personalized one-on-one technical support.
Fast response times within a few hours.
Most competitive pricing in the market—up to 30% lower than Europe and North America.
Materials Built for Rapid Tooling
Material | Key Properties & Applications |
---|---|
Aluminum | High machinability, ductility, and strength-to-weight ratio. Excellent thermal/electrical conductivity with natural corrosion resistance. Ideal for lightweight, precision components. |
Zinc | Slightly brittle at room temperature with a shiny-grey finish. Offers good castability and moderate strength for rapid tooling prototypes. |
Iron | Industrial staple, often alloyed as steel. High magnetic permeability, durability, and tensile strength. Used for hard magnetic applications and structural parts. |
Titanium | Superior corrosion resistance, biocompatibility, and strength-to-weight performance. Critical for aerospace, medical, and chemical industries. |
Steel | Versatile iron-carbon alloy with high tensile strength, heat/fire resistance, and moldability. Widely used in construction, automotive, and aerospace. |
Stainless Steel | High strength, ductility, and corrosion/wear resistance. Machinable and polishable, but harder and costlier than aluminum. Suitable for high-stress environments. |
Bronze | Exceptional seawater corrosion resistance. Best for low-stress, marine, or decorative CNC-machined components. |
Brass | Stronger than bronze with low friction and corrosion resistance. Perfect for marine mechanical parts and fittings. |
Copper | Unmatched electrical/thermal conductivity. High corrosion resistance and machinability, ideal for electrical components and heat exchangers. |
Finish | Description & Key Characteristics | Typical Ra (µm) | Best For |
---|---|---|---|
As Machined | Raw finish straight from machining, with visible tool marks and milling patterns. Cost-effective with no post-processing; preserves dimensional accuracy. | 0.8–3.2 | Functional parts where aesthetics are secondary. |
Bead Blasting | Uniform matte finish achieved with high-pressure glass/ceramic beads. Removes tool marks and adds slight texture. Non-reflective; ideal for pre-treatment. | 1.6–3.2 | Aesthetic parts, molds, or pre-painting prep. |
Sand Blasting | Aggressive matte/satin finish using abrasives (e.g., aluminum oxide). Removes rust/coatings; rougher than bead blasting. | 2.5–6.3 | Decorative or functional parts needing texture. |
Painting | Liquid or powder coating for gloss, matte, or custom colors (RAL/Pantone). Enhances corrosion resistance and aesthetics. Thickness: 15–100 µm. | Varies | Parts requiring color matching or added protection. |
Anodizing | Electrochemical oxide layer (Type II: 8–25 µm; Type III: 25–50 µm). Corrosion-resistant, dyeable, and maintains tolerances. | <0.5 (post-process) | Aluminum parts in aerospace, medical, or consumer goods. |
Plating | Thin metal layer (chrome, nickel, etc.) via electroplating. Glossy, durable, and improves conductivity/thickness: 5–50 µm. | 0.1–0.5 | Decorative hardware, wear-resistant components. |
Polishing | Mirror-like gloss achieved with abrasives/compounds. Reduces roughness to near-zero; labor-intensive. | 0.1–0.4 | High-end aesthetic or low-friction applications. |
Chromate | Chemical conversion coating (0.5–7 µm) for corrosion resistance. Conductive; colors include clear/yellow. | 0.5–2.0 | Aerospace, electronics, or as a paint base. |
FAQs of Rapid Tooling
Why Should I Use Rapid Tooling?
Rapid tooling accelerates prototype and low-volume production with cost-effective, material-accurate parts (plastics, metals, or rubbers). It’s perfect for:
Design validation and functional testing.
Market analysis with near-production-quality parts.
Custom finishes (e.g., anodizing, bead blasting) to match aesthetic or performance needs.
How Quickly Can I Receive My Parts?
* Prototype molds: 5–10 days.
* Low-volume production: 2–3 weeks.
* Contact us for an exact timeline based on your design.
What Materials Are Available?
* Plastics: ABS, Nylon, PC.
* Metals: Aluminum (lightweight), Steel (high-strength), or Stainless Steel (corrosion-resistant).
* Finishes: Plating, chromate, or painting for added durability/appearance.