SERVICES>DIE CASTING
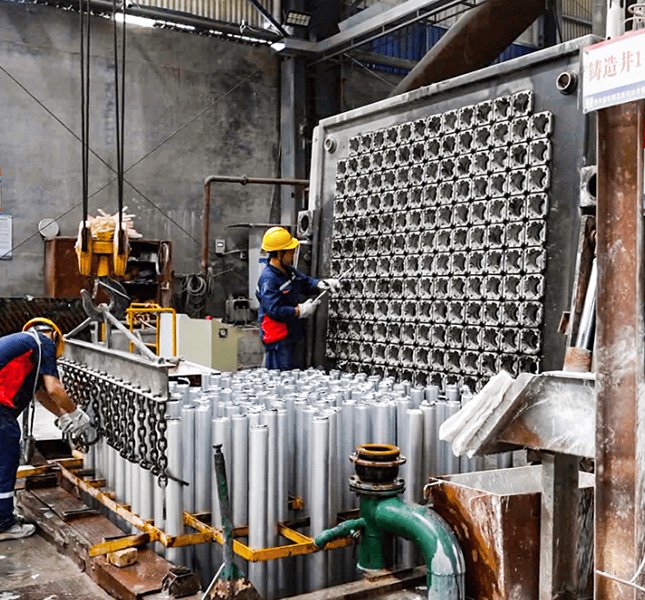
Premium Die Casting Solutions
This process enables the fabrication of intricate designs with tight tolerances, superior surface finishes, and consistent quality, making it well-suited for industries that demand durable and reliable components.Key advantages include:
* High precision and accuracy
* Excellent surface finish
* Versatility in material selection
* Enhanced durability and strength.
Best You Need, Best We Provide!
Reasons to Choose Our Die Casting Services
High-Quality Parts
FUTURE PRECISION, ISO 9001:2015 certified, delivers precision die casting backed by rigorous quality inspections at every stage—from material selection and pre-production to in-process checks, first article inspection, and final delivery. Our commitment guarantees exceptional excellence in every die-cast component.
Timely Delivery
With modern automated facilities and efficient workflows, FUTURE PRECISION ensures rapid production without compromising quality. Our die casting services combine punctuality with precision, consistently delivering orders on schedule.
With Competitive Price
We provide premium die casting solutions at cost-effective rates. While die casting parts generally have low per-piece costs, initial investments in tooling and maintenance are high. Our optimized processes maximize value without sacrificing quality.
Die Casting Specialists
Our experts excel in custom die casting, enhancing product durability and reducing costs. Using advanced machinery and tailored processes, we ensure every part meets your functional, aesthetic, and performance needs with clear, ongoing communication.
Knowledge & Experience
With decades of industry experience, our skilled team offers unmatched knowledge and hands-on expertise. Clients benefit from our deep understanding of die casting, ensuring every project achieves the highest standards.
Advanced Equipments
Equipped with cutting-edge die casting technology, we deliver consistent, precise results. Typical tolerances range from ±0.003″ to ±0.005″ per inch, with capabilities as tight as ±0.001″ depending on specifications, part geometry, and materials.
From Concept, Prototyping to Full Production
FUTURE PRECISION is equipped with state-of-the-art die casting machines and advanced technology, enabling the production of high-quality, on-demand parts for a wide range of industries. We specialize in the most widely used die casting methods, capable of producing components with complex geometries, tight tolerances, and excellent mechanical strength.
* Over 7 Years of Industry Experience;
* Certified ISO 9001:2015
* Quality Management System;
* CMM-Based Precision Inspections;
* Various Surface Finishing Solutions Available.
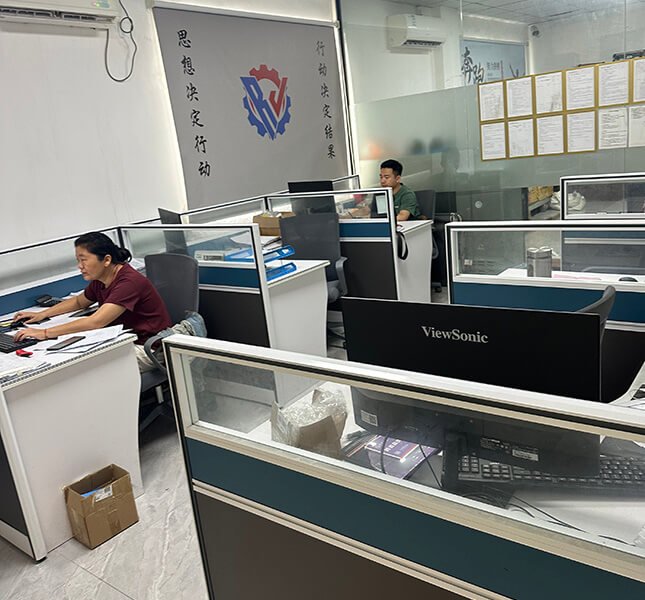
Custom Your Die Casting Solution
Custom-tailored Die Casting Services
Rapid Prototyping
We provide high-quality rapid prototyping services in China, offering more competitive CNC machining prices and faster turnaround times. Leveraging the latest prototyping technologies, our team works closely with you to address design challenges, validate and refine CNC prototypes, perform functional testing, and complete engineering verification.
Rapid Manufacturing
FUTURE PRECISION is your trusted die casting manufacturing partner in China. From rapid prototyping to full-scale production, we deliver tailored die casting solutions backed by extensive machining experience and strong resource integration. Our capabilities ensure that every part meets the highest standards of precision and quality.
Bespoke CNC Machining
We also offer one-stop rapid die casting services and cost-effective custom machining for short-run and prototype production. Whether you need production-grade materials, intricate geometries, tight tolerances, or fine details, FUTURE PRECISION Die Casting Factory delivers parts that match your exact specifications through every stage.
OUR HAPPY CUSTOMERS
We've Helped Thousands of Customers Succeeded
Get personalized, one-on-one support from our expert technical team, with fast responses within just a few hours. We offer some of the most competitive prices in the industry—up to 30% lower than those in Europe and North America.
Die Casting Craftsmanship
Material | Key Properties | Common Alloys | Primary Advantages | Typical Applications |
---|---|---|---|---|
Aluminum Die Casting | Lightweight, corrosion-resistant, excellent thermal conductivity | ADC12, A360, A380 | • 30-50% lighter than steel • Natural corrosion resistance • Complex geometries achievable • Cost-effective for high volumes | Automotive components, aerospace parts, heat sinks, electronic housings |
Copper Die Casting | Superior conductivity, antimicrobial properties | ZQA19-2, ZQA19-4 | • 95% IACS electrical conductivity • Natural antimicrobial surface • Excellent corrosion resistance • High temperature stability | Electrical connectors, heat exchangers, plumbing components, marine hardware |
Magnesium Die Casting | Lightest structural metal, good vibration damping | AZ91D, AM60B | • 75% lighter than steel • Excellent EMI/RFI shielding • 20% faster cycles than aluminum • Fully recyclable | Laptop cases, camera bodies, automotive steering components, aerospace brackets |
Zinc Die Casting | High precision, excellent surface finish, good impact strength | Zamak 3, Zamak 5, ZA8 | • ±0.025mm dimensional accuracy • Superior as-cast surface finish • 25% faster cycle times than aluminum • Thin-wall capabilities (down to 0.5mm) | Precision gears, hardware components, decorative fixtures, lock mechanisms |
Finish | Description | Key Characteristics | Typical Applications | Surface Roughness (Ra) | |
---|---|---|---|---|---|
As-Cast | Standard finish straight from the die casting mold | • Economical production finish • Visible tool marks and ejector pin traces • Minimal post-processing | Internal components Non-visible parts Functional prototypes | 3.2-6.3 μm | |
Polished | Mirror-like reflective surface achieved through mechanical polishing | • High-gloss aesthetic appearance • Reduces surface porosity • Improves cleanability | Decorative hardware Food service components Medical equipment | 0.1-0.4 μm | |
Sand Blasted | Uniform matte texture created by abrasive media impact | • Hides minor surface defects • Provides consistent matte appearance • Improves paint adhesion | Automotive interiors Industrial equipment Architectural fixtures | 1.6-3.2 μm | |
Anodized (Type II) | Electrochemical aluminum oxide layer formation | • 5-25μm protective layer • Available in multiple colors • Enhances wear resistance | Consumer electronics Aerospace components Marine hardware | 0.2-0.5 μm | |
Powder Coated | Electrostatic polymer powder application with thermal curing | • 50-100μm thick coating • Excellent chip resistance • Wide color selection | Outdoor equipment Appliances Retail displays | Varies by texture | |
Brushed | Directional abrasive finishing creating linear grain pattern | • Conceals handling marks • Sophisticated metallic appearance • Maintains metallic feel | Elevator panels Commercial signage Kitchenware | 0.4-0.8 μm |
FAQs for Die Casting Process
What Is the Die Casting Process?
* Mold Preparation: The die is lubricated and preheated to optimize metal flow and facilitate part ejection.
* Metal Injection: Molten metal is forced into the die cavity at high speed and pressure.
* Cooling: The metal rapidly solidifies within the mold.
* Ejection: The die opens, and the finished part is ejected.
* Trimming: Excess material (flash, gates, etc.) is removed for a clean final product.
What are the Advantages of Die Casting?
Rapid Production: Short cycle times enable cost-effective mass production.
Strength & Lightweighting: Dense, void-free metal structures provide durability with minimal weight.
Material Efficiency: Minimal scrap generation reduces waste and secondary machining.
What about Disadvantages of Die Casting?
Material Restrictions: Primarily suitable for low-melting-point alloys (e.g., aluminum, zinc).
Porosity Risk: Rapid cooling can trap air, leading to internal voids.
Size Limitations: Optimal for small-to-medium parts; larger components may sacrifice accuracy.
What are Key Design Considerations For Die Casting?
CNC lathe machining typically costs 15% less than 3-axis milling for similar parts.
5-axis machining is more expensive:
Continuous 5-axis milling costs >20% more than indexed (3+2) milling.
Costs can double compared to standard 3-axis milling. Pro Tip: Larger production runs optimize cost-efficiency by amortizing setup expenses.
How Long does It Takes for Die Cast Tooling?
What is the Standard Tolerences of FUTURE PRECISION?
±0.5 mm for dimensions up to 250 mm.
Tighter tolerances (±0.02 mm) are achievable with post-machining.
Note: Material choice (e.g., aluminum vs. zinc) influences shrinkage and final accuracy.
Is that Possible to Post-Machine the Die Cast Parts?
* Achieve tighter tolerances.
* Improve surface finish.
* Add complex features.
* Mitigate porosity-related defects for critical applications.